MCUs pack flexible features for EV control
NXP Semiconductors has unveiled its new S32K39 series of automotive microcontrollers (MCUs) optimized for electric vehicle (EV) traction inverter control applications at Electronica 2022. Targeting next-generation electrification, these MCUs address new EV requirements for networking, security, and functional safety as well as the industry’s move to zonal vehicle E/E architectures and software-defined vehicles. Together with NXP’s battery management system (BMS) and EV power inverters, they provide end-to-end solutions for next-generation EVs.
The S32K39 series is designed for modern electrification applications. The new MCUs can meet requirements for software-defined vehicles and zonal architectures with support for hardware isolation, time-sensitive networking (TSN), and advanced cryptography.
The high-performance S32K39 MCUs are optimized for high-precision control of traction inverters that convert the EV battery’s DC power into alternating current (AC) to drive modern traction motors. The MCUs accept the torque commands and precisely control the traction motor to smoothly accelerate/decelerate the vehicle.
“We are controlling the EV motion with a compelling combination of new technologies and a high level of performance,” said Brian Carlson, Director of Global Product and Solutions Marketing, Automotive Processing – Vehicle Control and Networking Solutions. “We integrate a lot of functionality that was external to the chip previously, so we reduce cost and start providing more flexibility with software.
“New architectures like zonal architectures require a new level of networking with Ethernet. Time sensitive networking is a key part of it, which allows you to distribute the processing across the vehicle in zones and have it deterministic, which is key for these functional safe applications,” added Carlson.
In addition, NXP added the security capabilities of it S32 family, which delivers a full complement of crypto technology to support end-to-end security and cloud connectivity, which is important for over-the-air updates, he said. “And, of course, functional safety. These have to use the highest levels of safety which is ASIL D for automotive.”
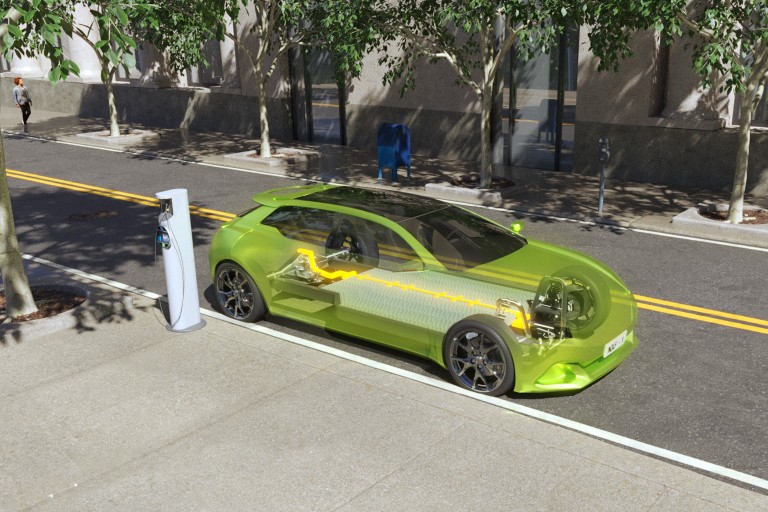
The S32K39 series addresses modern electrification applications. (Source: NXP Semiconductors)
Carlson said the new series addresses several EV trends, ranging from new architectures, scalability, and functional safety to range anxiety, cost, and efficiency. “The most important for a lot of people is range anxiety, so EV manufacturers always want to increase the efficiency of their vehicles, which improves the driving range,” he said.
By leveraging over-the-air updates, one of NXP’s customers has extended the range of its EV trucks by 20 miles. “Having the ability to not only support new technologies over time, but also existing vehicles in the field with new software updates that can improve control algorithms and make the EV more efficient and extend the range is important.”
Also critical is the highest level of functional safety, which is ASIL D, and going forward especially as vehicles become more autonomous, high reliability and availability are very critical, he added.
Scalability to multiple motor support also is an advantage, he said. Typically, EVs have single motors, while higher performance models may have dual motors or even three motors that gives higher performance and more horsepower, Carlson said. “We see some applications where OEMs will use four motors – two motors on the front and two motors on the back – that gives the ultimate handling of the vehicle and ultimate performance.”
Thanks to TSN Ethernet the S32K39 supports remote smart actuation. This allows NXP to leverage the previous processors that control the vehicle like the S32E, for example, to extend electric vehicles from not only single or dual motors but also to three and four motors, which provides a lot of advantages in performance and handling in electric vehicles, said Carlson. This gives car makers the flexibility to support in a scalable way various configurations of motors, he added.
Changes in vehicle architectures also require new technologies. “Car manufacturers are moving to zonal architectures that go from having boxes – ECUs – all over the car into a handful of boxes like a central compute and four zonal controllers, which control the functionality of vehicle, requiring new technologies to support it.”
Reducing overall costs also is a big trend, he said. “With EVs we’re trying to drive the cost down and that means new technologies and components. You need a controller in the traction inverter that can adapt and be able to support upgrades into the future. It has the performance capabilities and the control capabilities to support new technologies as they become available over time.”
S32K39 features
All of these trends had an impact on how NXP designed its controller for EV motor inverters.
“There are lot of dynamics in the EV market and what the inverter has to do because it’s the heart of everything. The S32K39 is designed to address all of those [trends], provide some future proofing, and allow OEMs to scale their architectures in an intelligent way,” said Carlson.
Key features of the S32K29 family include four Arm Cortex-M7 cores at 320 MHz configured as a lockstep pair and two split-lock cores, up to 6 MB of flash memory and 800 KB of SRAM, and an integrated DSP for flexible digital filtering and machine learning (ML) algorithms. It also features two motor control coprocessors and NanoEdge high-resolution pulse-width modulation (PWM) for precision control. The new controllers also support multiple switching technologies – insulated-gate bipolar transistors (IGBTs), and newer silicon carbide (SiC) and gallium nitride (GaN) devices.
The S32K29 also incorporates a hardware security engine (HSE) for trusted boot, security services, and secure over-the-air (OTA) updates using public key infrastructure (PKI) and key management.
The hardware security engine is important as part of the modern MCUs to support end-to-end security from the cloud to the vehicle with the latest public key infrastructure, so not just the symmetric cryptography but also asymmetric cryptography like RSA and ECC, said Carlson.
The motor control coprocessors also are another key feature of the S32K29. They offload the Arm cores to do more things like vehicle health prognostics, data analytics, and other value-add capabilities within the inverter, said Carlson.
The high-resolution PWM – down to 195 picoseconds – is a new innovation with the S32K29 family and it provides better efficiency, he added. “To maximize the energy efficiency and smooth the PWM – the pulses that the controller has to send over to the inverter as it converts DC to AC – the better you can create that signal the more efficient it is.”
The integrated DSP is important for doing customized adaptable filters rather than what is typically done externally in hardware with capacitors and resistors that isn’t configurable or in chips with very limited configurability, said Carlson.
The DSP offers total control for filtering as well as doing things like machine learning for anomaly detection, vehicle health prognostics, and monitoring signals for anomalies, he added. “It provides added value for our customers, especially in these modern applications where they want to do more customizations and software-defined over time to improve performance. “It’s not just a fixed filter, it gives them the ability to update over time.”
The MCUs also incorporate an ASIL D software resolver, along with integrated sine wave generation and sigma delta converters, which eliminate external components for reduced overall system cost. They also provide six CAN FD interfaces and many advanced programmable I/Os.
“The software resolver allows this controller to determine very accurately the position of the motor rotor and the velocity, which allows it to give very high precision control back to that PWM – it’s a feedback loop – so that works in conjunction with it,” said Carlson.
But he said the biggest value is the elimination of the external components and related circuitry. “Today, a lot of vehicles use an external resolver-to-digital converter, or RDC, which typically costs $2-3 with discretes around it, so we now move the functionality into this part, and we do it with ASIL D, the highest level of safety, to reduce the cost and increase the performance so it’s a really strong value add.”
The S32K39 can control dual traction motors with 200-kHz loops at the same time, improving efficiency for smaller, lighter, more efficient inverters, which translates into a longer driving range. “It supports two 200-kilohertz loops, so we’re supporting dual motors, and with 200-kHz we can support future technologies and newer and faster transistors, which drives lower costs because the components can be smaller,” he said.
Carlson noted that the market is moving to faster switching with SiC, from IGBTs, which are predominantly used today. “With higher switching, we also start to support higher phases, so that will come over time.”
The MCUs also can control six-phase motors with increased power density and fault tolerance for improved long-term reliability. “Support for multi-phase motors ties into the higher reliability and availability,” he said.
Carlson sees interest in moving to six-phase motors from three phases typically used today. “With six phases if one of the phases goes out you still have five others and it’s not going to stop the motor. You still have higher reliability and that means it’s a better product at the end of the day,” said Carlson.
The S32K39 can control up to quad traction inverters when coupled with the NXP S32E real-time processor and can implement advanced traction capabilities for 4-wheel drive EVs in this configuration.
“If you look at all the combinations, the S32K39 is very compelling versus other options which have gaps, whether they don’t have the TSN, or they don’t have sufficient memory to do multiple applications at the same time, or they can’t do dual motor control, or do the software resolver in a safe way, so that’s the big value, bringing all of those together in a single device,” said Carlson.
It also gives NXP’s customers a path from the previous generation PowerPC processors to Arm-based processors, he said.
Thanks to the family’s flexibility, the S32K39 series, with the S32K37 variant without the motor control coprocessors, is well-suited for other EV applications, including battery management (BMS), on-board charging (OBC) and DC/DC conversion.
The S3239K MCUs are available in two packages: the 176LPQFP-EP and 289MAPBGA. The S32K37 versions without the two motor control processors also are available. Production release is planned for the fourth quarter of 2023.
Engineering samples, evaluation boards, reference designs, and a set of software support and tools are now available for lead customers. The S32K39 MCUs can be combined with the NXP FS26 safety system basis chip (SBC) and the advanced high voltage isolated gate driver GD3162 with adjustable dynamic gate strength control for a safe inverter control system. Both support ASIL D for traction inverter development.